Features & Specs
FASM-B High Performance Films Applying & Sticking Machines
Introduction
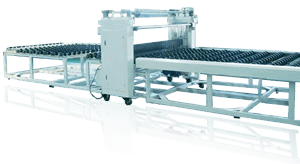
Some glass, for example reflective coated glass, requires protective films adhering on glass surface. FASM-B series film adhering machines are used to apply film layers on glass surfaces. Machines are operated off line or inline incorporated with upstream production lines such as glass coating system. Some glass is required to applied films on both surfaces. FASM-B is available with optional double side adhering capability by passing the machine in one time. Mirrors back are also adhered with protective films for safety purposes. The machines are also mirror back film applying and affixing machines.
Options
Automatic Film Cutting
Film cutting device is composed of a pair of pneumatic cylinder, electromagnetic cutch and heating wire. Heating wire is installed transversely to glass travel direction. After film sticks on glass or mirror from leading edge till tail edge, glass stops on outlet conveyor. Heating wire is activated by pneumatic cylinders automatically and film is then cut. Glass transportation is then activated manually by switch on panel or foot pedal. Glass transportation starts automatically in online film sticking machines.
Double Sides Films Gluing
Some glass requires both surfaces applied with films. This option includes two film supports and film stretcher installed beneath conveyor rollers. Top and bottom surfaces of glass are affixed with films at the same time.
Film Protective Layer Winding
Some films are surface protected with a thin layer. When film is applied on glass, this protective layer is no more necessary and it is peel off. This winding system is used to peel off and wind up the film layer automatically when film is being applied on glass. Winding speed is synchronizes with rollers conveyor speed.
Inline Film Affixing
The film attaching machines could be incorporated online with buyer's existing machines forming a continuous production line. When glass is processed, for example, reflective coating, by upstream machines, glass is applied with films in this machine. This inline design eliminates repeated glass loading and unloading. When this option is selected, inlet and outlet conveyors are excluded. These two conveyors could be included at buyer's disposal. The film application machine shall be inserted in between buyer's upstream and downstream conveyors. Speed of inline film adhibit machine is adjustable so that it is always synchronized with buyer's upstream and downstream conveyors.
Specifications
Models | FASM-B-1200 | FASM-B-1600 | FASM-B-2000 | FASM-B-2500 | FASM-B-3000 | FASM-B-3300 |
Max. Glass Width (mm) | 1200 | 1600 | 2000 | 2500 | 3000 | 3300 |
Max. Glass Length (mm) | 2200 | 2700 | 3200 | 3800 | 6000 | 6200 |
Min. Glass Width (mm) | 300 | |||||
Min. Glass Length (mm) | 600 | |||||
Glass Thickness (mm) | 3 ~ 19 | |||||
Top Press Roll Rotation | Idle | |||||
Top Press Roll Vertical Movement | Idle | |||||
Bottom Press Roll Rotation | Motorized Driven | |||||
Bottom Press Roll Vertical Movement Activated By | Pneumatic Cylinders | |||||
Bottom Press Roll Vertical Stroke Length (mm) | 40 | |||||
Press Roll Diameter (mm) | Φ 200 | |||||
Press Roll Rubber Thickness (mm) | 15 | |||||
Rubber Shore Hardness | 80 | |||||
Glass Speed (m/min.) | 2 ~ 10. | |||||
Inlet / Outlet Conveyors Rollers | Idle | Motorized | Motorized | Motorized | Motorized | Motorized |
Conveyor Rollers Transmission | Manual | Chains with Sprocket Wheels | ||||
Conveyor Rollers Distance (mm) | 300 | |||||
Working Height (mm) | 900 ± 20 mm | |||||
Voltage | 380V / 3 Phase / 50Hz | |||||
Power | 2.1 | 2.1 | 2.1 | 3 | 3 | 3 |
Inlet Conveyor Length (mm) | 2000 | 2500 | 3000 | 3600 | 5800 | 6000 |
Rubber Press Roll Section Length | 1000 | |||||
Outlet Conveyor Length (mm) | 2000 | 2500 | 3000 | 3600 | 5800 | 6000 |
Outer Dimensions (LxWxH) (m) | 5 x 1.9 x 1.8 | 6 x 2.3 x 1.8 | 7 x 2.7 x 1.8 | 8.2 x 3.2 x 1.8 | 12.6 x 3.7 x 1.8 | 13 x 4 x 1.8 |